-
-
-

Why not made in USA?
We get asked this almost daily. A number of people get rather agitated when told many of our products are not made in America- especially when it comes to reproductions of US military gear and uniforms. Sometimes it gets pretty funny- threatening to expose us for fraudulent advertising because the "US" in "US M1943 Field Jacket" means we're claiming it's made in America or the "USA Made Items" tab on our navigation bar is obviously put there for deceit. When we point out that the item in question has "imported" in the description...."you just put it there! It wasn't there a minute ago!!!"
As to the question at hand, the short, honest, answers are, one it's far too expensive, and two, in many cases it's no longer possible to do at any price. The upside is that, with detailed specifications, the companies on the other side of the Pacific are perfectly capable of making clothing of equal (or better) quality than what we can do here- and for a lot less.
I've made reproductions for 30 years. I wish things were otherwise, that made in USA still meant what it once did, but I deal with reality every day, so here's how it is.
Cost: Aside from a vocal minority, most people appear to realize that the factor that drove our garment industry to its grave was cost. Wages in Asian sewing factories average about 10% of those in the USA. Currently, overhead (hourly cost: wages + rent + utilities etc) is $2.50 per hour. In our shop it's about $25.00 per hour.
This effects both the assembly of the garments themselves, as well as the cost to weave, finish and dye the fabrics. This translates to an immense per garment cost difference, with the gap widening exponentially as the labor time increases for complex items.
Typically, the same article made here will have to retail for 300% more than the identical item made "over there". Those things that can be made quickly, like t-shirts, have a smaller price disparity while others, like field jackets or German tunics will have a far greater price gap. Just to sew a German tunic will cost us $200-300 in the US. In China the same job can be done for $25 or less.
Feasibility is no longer there: The garment industry largely fled our country 25 years ago. As they left, the supporting industries gradually followed or closed due to lack of customers. This includes sewing equipment sales and service, thread suppliers, button & zipper firms, dyers & finishers, camouflage printers and the mills that make the fabrics. As of now, 2020, we can only acquire one or two types of the fabrics we use from American mills- and one of those told us that they will likely close down soon. This means, that to have truly American made items that are sewn and sourced in this country (as people expect the term to mean) is nearly impossible.
They're honestly as good or better: Over the past 10 years, the foreign contractors have met and exceeded the quality we once had here. Many mills invested in the best German, Italian and American weaving machinery. The sewing plants have top quality sewing and cutting equipment, and technicians trained in the US and EU. Their dyeing and color matching in particular are better than what we used to get from the plants in New England. (I suspect tight EPA regulations for dyes and chemicals may have been a factor.)
Our biggest hurdles now are convincing them not to make any "improvements" in the garments and persuading them to do historically correct things that, in their eyes, amount to intentionally defective quality such as with printing German camo.
The most telling opinions were from the girls in our factory. Several have been sewing for over 50 years. They spot-check the shipments of imported garments and make minor repairs when or if necessary. Lately, all they have had to say about what's come in is "Darn they make nice stuff. This is better than what we made." This is no joke or exaggeration.
We still make many things here- for now: When it's possible, and financially viable, we do make it (or have it made) in this country. But we're constrained by more realities than simply material availability and labor cost, so how long this will continue I honestly don't know. Our largest contractor is struggling to remain staffed after instituting drug testing, another webbing supplier just went under, and mortality is threatening us. Half of our sewing staff is 70+, and the only two sewing machine mechanics left in our region are both nearly 80. Finding replacements is proving a quest of biblical proportions.
-

We are asked on a daily basis why more or all of our products aren't made in America- a hardly illogical question since we have our own sewing factory in the building. However, there are several reasons we do not and cannot make or acquire all of our products in the USA (or Europe.) This post will give a detailed explanation, based on 25+ years experience in selling, manufacturing and contracting reproduction WWII militaria.
Although most people are simply curious, a few types are a bit belligerent about the entire subject, insisting that we are somehow unpatriotic and disloyal to our country for manufacturing things outside our nation's borders. Others try to be helpful and point out that the patriotic fervor of customers would lead to increased sales were we to produce everything here. It's always great to be offered expert advice from those with less than zero experience in garment manufacturing.
These are facts and actual experiences- not platitudes and proclamations based on emotion or patriotic fervor.
Price: Yes, most people understand that cost is the number one reason so much is not made in this country anymore. Despite all the blabbering of the politicians and news media that make it seem to be a simple matter to "just" make it in USA, the truth is far different. Labor cost is Asia runs about 1/10th (or less) of that in America. Fabrics are typically 30-50% cheaper. This means that a German tunic costs $40-50 from China- the same tunic, made in America, costs $300-400, simply due to the difference in labor and materials. "Cost" is what a business pays for the tunic- the retail price will typically be double or triple that. Depending on labor time, American made garments generally cost at least three times more than the same item made in Asia.
Retail Facts: Would you pay three times as much for the same jacket ($99 vs. $300) just because it was made in USA? Even if the quality isn't quite as good, the $99 jacket will win 98% of the time. We have over ten years of collated sales figures on numerous items, and price is the key on all but a few rare (and sometimes surprising) things. Although both were made in China, when we switched the wool lining in the M41 Field Jackets from wool to cotton flannel, and the price dropped 35%- despite the howls of protest from the history nerds that we should be boycotted for dishonoring our forefathers- sales of the jackets went from 300 annually to nearly 1,000. If we made M41's here, they'd be at least $250. Quality would be the same and we'd be lucky to sell 5 in a year.
For a more direct comparison, take German tunics. Our imported models were $150, and we sold about 500 annually (all styles combined.) Texled tunics, made in USA, wool from Deutschland, original thread and parts, etc, etc, were $750+. We sold about 1.5 per month. So 20 vs. 500. The profit margin on the imported ones was far better- Texleds should have been double that price and then they might have been worth it.
The higher the price, the greater this disparity in sales numbers. It seems that $100 is the tipping point- and if the American made version is no more than double the price of the import, and it retails for under 100 bucks, they can be viable products. So, USA made fieldgear sells at a rate of 30-50% that of the cheaper imported items, and the lower the price, the higher the ratio. American made carbine pouches sell almost 1-1 with the imports ($20 vs. $10), while cartridge belts are about 1-3 ($100 vs. $60).
Quality: Manufacturing clothing is not rocket science. The Asians are brilliant, industrious people and they are perfectly capable of producing garments as good or better than we can- and they often do. The problems we have had regarding patterning and assembly were most often miscommunications or lack of oversight on their part with their workers. When properly supervised, their people make just as good a product as we do (did). We had some epic f*ck ups ourselves when we made garments- and I mean EPIC. The difference is that I was there on site to stop and correct it when a worker got a bright idea to move the buttons or swap sleeves. Most of the time, they do catch and correct the antics in time.
Conversely, I have examined a number of American made garments in recent years, usually when a red blooded type is showing it off trying to convince me that we should emulate "this" company. In no case was I impressed (actually much to my chagrin) and in one case (a very well known company that makes men's pants) I was horrified by the dismal sewing quality. In many cases, made in USA was not even as good as made "over there".
Materials: We opened the sewing shop in 1999. At that time, there were still a good number of fabric mill left in North America, although they all told me that they were barely hanging on. Now, 20 years on, they are all gone. So, even if we decided to manufacture clothing here again- we can't get the fabrics. We'd have to get them from- horrors- "those" people. Buttons? Zippers? Ha.
Moreover, in our experience, the fabrics and fabric finishing done overseas was superior to what we were once able to obtain in this country. About 25% of the time, the American made fabrics turned funky colors within an hour of exposure to the sun. Fabrics from China? Never. Not even once.
If quality is equal overseas, why do we still make some items here?
In general, for items under $100, making them in this country can be viable. In many cases, due to the short labor time (especially as opposed to most garments) we can almost compete with the foreign US fieldgear items which means ours are only twice as much- instead of 3-10 times more. This also allows us to rapidly restock when we run out, rather than waiting 6 months to a year for things ordered from overseas.
US Fieldgear: For some reason, the Asians can make killer hardware, webbing and canvas, but combining them is another mystery of the universe. If they can make nice German tunics, then surely a Musette Bag is a cinch. Right? Apparently not. Covers that no canteen will fit in, cartridge belts with ten useless pockets, hooks on backwards, eyelets that snap the first time you look at them.... Only in the past 2 years have we managed to get decent reproduction gear from China but still not quite equal to what we can do here.
Boots: Footwear is the toughest and most expensive of all things we have made. No matter what we do, the reproductions made anywhere in Asia have issues- this is often due to the suppliers frantic quest to cut costs so they use substandard or rotten leather, skip steps (like nailing on the heels) and generally fuck up anything they can. For the time being, we have given up on making boots overseas. Thus far, the only places that have been able to consistently make boots that really last are the US and Mexico. They are 2-3 times as much as Asian made, but they can last a lifetime rather than 3 weeks. Or days. That said, many people seem to prefer buying a new pair of $150 boots every six months as they fall apart rather than one $300 pair.
Yes, most shoes ARE now made in Asia and many hold up just fine. There are two things at play here- one, soles are now bonded on, rather than stitched, which is faster and holds up just as well. Next to no one over there is set up to sew them on anymore. Second, this requires the soles be made in a mold- and those cost about $10,000 per size. So, if we want to make good quality but affordable repro jump boots in China, Vietnam or Indonesia, the upfront cost is about $100,000. They wouldn't be 100% authentic, but if they were $75, looked good from 5ft away and held up, 98% of reenactors wouldn't care.
So this is the long and honest answer as to why we're pinko commie traitors. Even if we could make it all here, next to no one would pay for it and we'd be unemployed.
-

Jacket, Field, Pile, O.D.The M1943 Field Uniform, which, with gradual updates, remained in production for the US military for over 40 years, had a rather controversial and tortuous birth. Despite apparent utility of the design, numerous high ranking officers attempted to stop or sabotage production repeatedly due to differing personal preferences, mostly regarding "soldierly appearances". One of the most embattled components of the new layered uniform was the liner. After months of testing, a pile lined jacket with knit cuffs and collar was decided upon by the QMC. However, another faction within the US Army continuously lobbied for the Ike Jacket to become the new uniform instead- when that battle appeared lost, they insisted that the short wool jacket be used as the liner. Months of bickering ensued which caused repeated production delays, ultimately causing a critical shortage of M1943 Field Uniforms in the Fall of 1944. This resulted in liner production to beginning in the Summer of 1943, followed by a gap in new contracts (while the generals battled to get some other uniform more to their liking produced instead) with new batches not being started until the following Summer. Issue of the liners was by no means universal, with many soldiers wearing sweaters or other jackets to accomplish the same purpose. Given that the liners have a sturdy outer shell, they were often worn on their own without the field jacket. In period photos, they can often be mistaken for tanker jackets unless the front is visible. allowing one to see the buttons.
The first liners were spec number 368A, Jacket, Field, Pile, O.D. approved 30 June 1943, with the contracts dated in late July. Quantities made are unknown, but I suspect they were substantial, given that 75+ years on, original examples are not terribly rare. The liners generally appear to be a rather ugly child born of a B15 Flight Jacket and the mailman. The shell is O.D. 7 cotton poplin, similar (if not the same) as that used on M41 Field Jackets, with two slash pockets. The interior is lined with woolen pile, and the neck and cuffs are trimmed with knit wool to prevent the wind from entering. The fronts is closed via 6 large plastic buttons, fastened through cord loops rather than buttonholes- likely due the difficulty of sewing buttonholes through the pile and impracticality of zippers for troops likely to be wearing gloves in freezing conditions. No provision was made to attach the liners to the field jackets themselves- they were simply worn as one coat over another.
In March of 1944, the design was amended slightly, with the new contracts being issued starting in May, as spec. 368B, as Jacket, Field, Pile, O.D. Type B. Some spec labels describe these as "Pattern B" in addition to or in lieu of "Type B". All Type B's appear to have an instruction label added below the size tag at the neck. Additionally, some 368B's have the pile lining covered with a layer of OD3 cotton twill (the fabric used for Tanker Jackets and Jump Uniforms). Examples of this type with the "khaki" interlining, to date, were all from the May 1, 1944 contract. 368B's from subsequent contracts have all had the more typical exposed pile inside. Despite the substantial difference in the design, the spec labels make no mention of it and all 368B's share the same spec and stock numbers regardless of interlining.
Later production runs of 368B's appear to be identical to the 368A's from the previous year aside from the instruction label in the neck. In the liner produced in the immediate postwar period, the pile lining was again covered, but this time with a nylon or rayon fabric instead of the cotton twill of the early 368B's. Given that the liners have a sturdy outer shell, they were often worn on their own without the field jacket. In period photos, they can often be mistaken for tanker jackets unless the front is visible. allowing one to see the buttons.
-

Original M1942 Paratrooper Uniforms
The M1942 Paratrooper Uniform is perhaps the most iconic of all WWII US uniforms. The intense interest in all things "airborne" has created a flood of reproduction jump uniforms in the past decade. Originals can now fetch over a thousand dollars, while the handful of reinforced suits command well over ten thousand. Many people have never handled or examined one, so this page will show original samples to help better educate the enthusiasts.
The information provided here consists of the observations I have made of originals over the years. I have owned and sold about two dozen original jump suits over the past decade. As a manufacturer I tend to notice details most collectors do not- in reality, they simply have no need to. They are not trying to figure out how to duplicate and re-assemble a uniform. The unissued uniform we initially copied in 1998 is long gone. Currently I have jackets in sizes 38L, 40R, and 44R. I have owned all the regular sizes (34-44) and measured them all to make sure our patterns were correct.
The jump uniform was developed in 1940-41 as a special purpose suit for the new airborne arm of the Army infantry. Several of the first officers in the paratroops collaborated with the War department to design the garments. After some trial and error, the initial idea of a coverall was discarded and the jacket and trouser adopted. The first version, known as the M1941 was similar to the M1942, but the pocket flaps had only one snap, the belt was sewn to the body of the jacket and the back vent was different. This was quickly modified into the M1942.
All photos are of original uniforms
|
|
Nearly unused original jacket. Worn by an instructor at Ft. Benning in 1943-44.
|
Shade variations
|
The jump uniform was made from 8 oz. cotton twill. This fabric is also used for the shells of tankers, Arctic M41's, some Mackinaws and a handful of M41 Field jackets. The wool overcoat also uses it for a lining. It is tough, but relatively lightweight. The twill is not nearly as heavy as denim. The color was olive drab no. 3, which is often erroneously called "khaki" by novices. The actual color varies widely from uniform to uniform- it ranges from grass stain green to a golden tan. Faded uniforms generally look more "khaki".
|
|
December 1941 spec for the jump jacket. Note the size tariff.
|
Materials list. Obviously, some changes were made after this was printed. I've yet to see oxidized bronze snaps...
|
The jackets were made in even sizes 34-44, regular, long and short. No, they didn't make odd sizes then either...
|
|
|
Typical main zipper. Conmar.
|
Knife pocket zipper- usually Conmar or Serval.
|
Armpit vents
|
The jacket has 4 angled pockets- the lower ones being slightly larger than those on the breast. Small pockets for pens or pencils are provided inside the breast pockets. Note: the shape of the pocket flaps varies from maker to maker- some have very sharp corners, others are rounded. The front is closed via a zipper- usually a Conmar or Prentice, but Talons have been observed. At the throat, a small pocket is built into the placket to hold the switchblade. In case of being entangled in his parachute harness or suspension lines, this location would be accessible for the trooper- unlike his hip or jacket pockets which were covered by the harness straps. This pocket could be opened from the right or left side by operating a pair of small zippers- most commonly Serval or Conmar brand. Four air vents are provided in the armpits- early jackets used sewn eyelets while later ones tend to use metal grommets like HBT caps.
As for modern zippers- Conmar and Talon are now just names one pays to have stamped on zippers. Originals used stamped brass or steel- today only cast pot metal is available. I have been looking for a company that can do the stamped brass for 15 years and so far no luck. The "brass" is simply a gold colored plating- it looks like cheap costume jewelry- so we use dull steel Talons on our uniforms. It's the closest thing we can get and they look good.
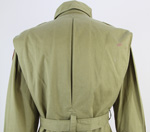 Bi-swing back
The back of the jacket featured a "bi-swing" back- a series of long pleats allowing the uniform to expand when the trooper needed to move his arms. A belt was provided at the waist to keep the jacket close to the body. Most early paratrooper uniforms busied themselves trying to avoid catching wind and bellowing up- when in practice the soldier's field gear and parachute harness took care of this.
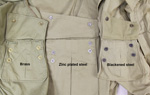 Snap variations
Both the jacket and trousers used press snaps to close the pockets, cuffs, collar and epaulets. All snaps used blackened caps. However, the parts underneath vary depending on when the uniform was made. The early production suits used brass (often very poorly set), most used zinc plated steel (which turns gray with age) and a few late examples have black steel. The finish on the cap has often worn off of heavily used used uniforms leaving them brass or steel in color. But when new they were blackened. As for our reproductions, I prefer the zinc type as they are the most common, and with some wear and tear they will begin to oxidize and look old. We have to special order them from Scovil- and they aren't cheap.
Jacket Production Variations: The jump uniform was only in production for a little over a year (42-43). There are two main groups I have seen. The early jackets may have been largely made by one company. The have no spec label (thus we don't know the company or date), but they have brass snaps, darker o.d. thread, and tend to be greener in shade. The snaps are almost always poorly set. The jacket at the top of the page is one of them. I have owned about 6 over the years, several being unissued. The later, more common jackets are very consistent, varying mostly in snap type and pocket shape (sharp or rounded corners). Makers include Sigmund Eisner and Goodall.
Jump Trousers
|
|
|
|
Button fly, watch pocket, narrow belt loops and suspender buttons
|
We didn't forget the button- the War Department did.
|
Pocket size and shape varies slightly between trousers.
|
Spec label is usually on the underside of the right front pocket lining.
|
The jump trousers were very similar in cut to today's BDU trousers. They were made in even waist sizes from 28-36. The shell was the same 8 oz twill as the jacket and the pocketing was white, unbleached twill or poplin. Belt loops and buttons for suspenders were provided. On each hip was a large cargo pocket with a bellows. Two slash pockets were provided at the waist and two on the rear- the left one being the only one secured with a button.
Early production jump trousers had a V-shaped panel of wool knit at the cuff to facilitate tucking them into jump boots. Later trousers dispensed with this feature and had a simple, slightly tapered ankle with binding tape.
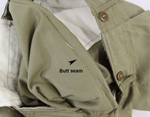 Inside of butt. Note stitches already pulling loose.
The jump trousers had one marked weak spot- the butt. The rear center seam was closed with a single stitch- it should have been felled (folded on itself) and sewn with a double needle. This led to constant blow outs. Most original trousers show repairs in this spot. Our trousers usually have extra stitching at this point to help prevent blowouts. (I say "usually" since as soon as I say "always" someone will prove me wrong. I check them at random and so far all were good to go.)
Reinforced Uniforms: (Like an idiot, I sold my reinforced uniform several years ago when I was offered an insane amount of money for it, so no photos at this time.) If someone has good clear pictures of their original reinforced uniform I'll be glad to post them.
After the first combat operations in North Africa and Italy, it became apparent that the M1942 had some weak points as the cotton twill was not heavy enough for the rigors of combat. If a trooper had a hard parachute opening, the shock caused the contents of his pockets to literally explode through the cargo pockets. So, in the Spring of 1944, the 82nd and 101st initiated a crash program to reinforce the jump suits of troopers going to Normandy. Each man was told to turn in his most worn out suit to be altered. The divisional riggers (parachute packers/ repairmen) acquired some heavy canvas and added patches to the pockets, elbows and edges of the cargo pockets of most men's suits. The canvas is rather unique- it is not normal olive drab G.I. material. It tends to fade to a grayish tint and has some sort of water proofing. It's similar in color to Austrian duffle bags for those of you who know what they look like. Perhaps it was some sort of aircraft cover fabric? The sewing on the reinforcing tends to be rather sloppy- after all, it was sewn in a hurry by teenagers who likely had a hangover. Crooked seams and uneven panels being the norm. Quite frankly, it usually looks like sh*t. If we duplicated that, we'd get a lot of returns with people howling "it's falling apart!".
To imitate the original cloth exactly is nearly impossible. For one, I don't have a piece of it to send the mill. I'm not going to ship off a $10,000 jacket. Second, to custom weave a fabric is usually a 5-10,000 yard minimum. Canvas is $5-7 per yard....do the math. Lastly, if it was the digny gray-green like originals, many living historians would probably complain that is wasn't "OD" and therefore wrong. For those of you who do know what originals look like- please know that I know too. But it's just not practical. I am truly sorry- I wish it were.
|